The anatomy of building
Jerry Tyrrell is a passionate advocate, assessor and champion of the Australian building industry. In this latest column he discusses the fundamentals of the industry to ensure every building could be better quality and cheaper, faster and easier to build.
Our industry is at a crossroad. Good choices and opportunities along one road, but so many speed bumps and dead ends up the other. Sadly, we are ultimately responsible for any obstacle we face or put up with. If we want change, we need to be strong and persistent – like we’re swimming against the tide.
The main problems we face are:
– Confusing and inaccessible rules and standards.
– Conflict based processes to solve disputes.
– Fragmented associations who look after their own interests.
These three issues make me really cross. Builders are working so hard to build well and there are so many groups gouging and obstructing what they do. Solutions are the only way forward. Otherwise, these self interest groups will keep making us shoot ourselves in the foot.
Possible ABCB solutions | ||
Action | Specifics | |
Stage 1 | Make access to the National Construction Code (formerly BCA) free. | This is the first step for everyone to accept, access and become familiar with this vital document. |
Reorganise structure of the National Construction Code. | Simplify the confusion, remove everything irrelevant to participants and summarise and illustrate everything e.g. objectives and principles – all materials, products and completed works shall be safe, dry, compliant and fit for purpose. | |
Provide a single resource online – under 100 pages combining:
• Requirements for all 10 Classes of buildings. • Summarised requirements of the relevant Standard or link to specific section in Standard. |
Structure of NCC to be:
• Classification of buildings • Safety – Structural adequacy under all loads (dead, live, catastrophe) – Personal • Performance – Best practice rules e.g. generic widths, heights, setdowns, slopes, slip resistance etc – Links to specific best practice details – Anatomy of building |
|
Stage 2 | Associations band together with Offices of Fair Trading. | All these groups need to combine resources and drive towards the same outcome – best practice. This will seriously reduce industry overheads where 5 or 6 identical products are currently being delivered different ways with the excessive overheads being paid by us. |
Stage 3 | Lawyers agree to act for both parties in the initial stage of any dispute. | A joint lawyer can usually steer parties towards a solution. Separate solicitors can keep parties apart as they generate paper, conflict and endless monthly bills for themselves, the experts and barristers. |
Stage 4 | Create the best practice details. | This is such an easy thing to do if there is will to do it – see Anatomy of Building below. |
CSI building
So many serious professions are self-critical and forensic about any mistakes, failures or patterns of problems.
When a crime happens, intensive forensic analysis starts. When a plane crashes, the crash investigation team does not stop until they know what went wrong. When a child dies, the pathologists and coroner want answers. If a bridge collapses, the engineers and scientists measure, calculate and reason why.
Yet Australia does not have a central database or register of building failures. The insurers don’t tell us about the materials which have failed and why the builder had to go back and do expensive remedial works. And the BCA is not based upon a hierarchy of actual risk. For instance, slips and falls kill so many more people than fire. We do not know if poor maintenance access is injuring and killing more people than any other cause. No one can tell us the financial benefit, if any, of using more durable materials.
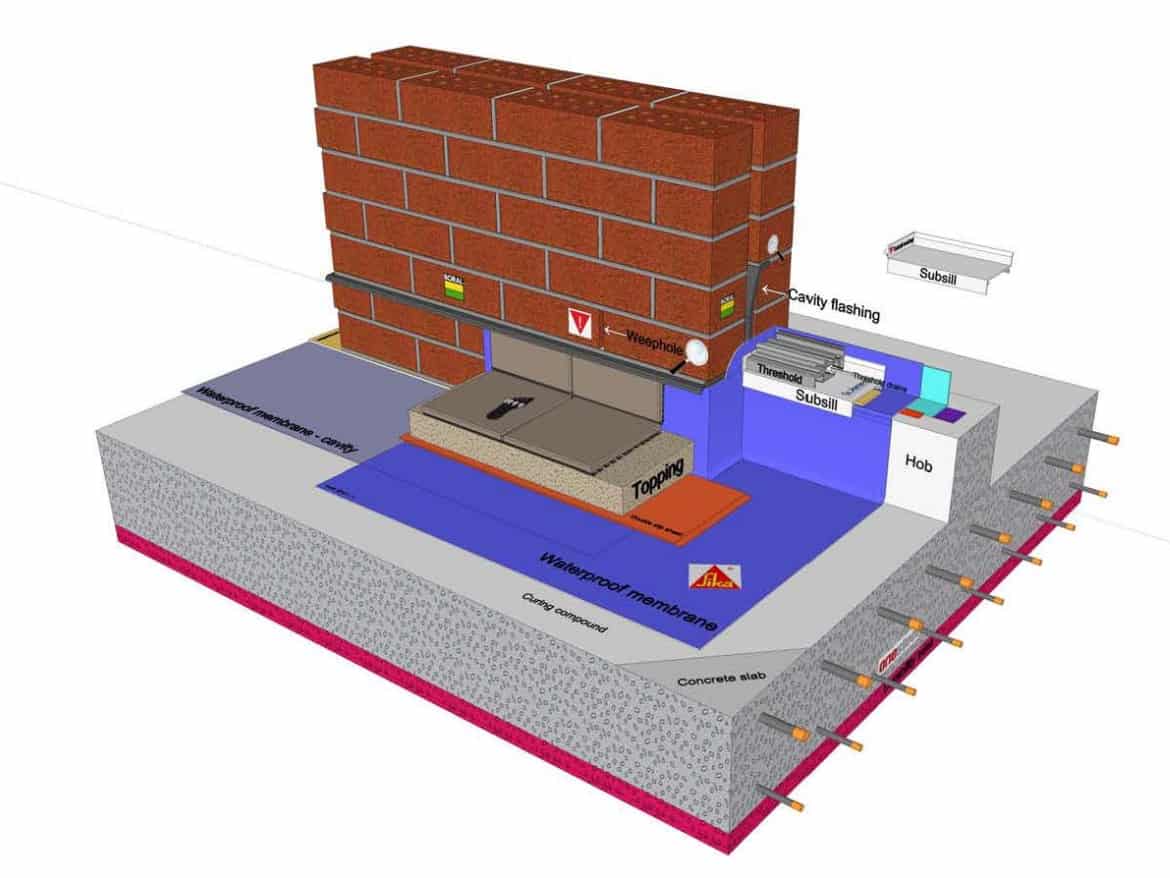
Anatomy of building example.
The UK has the Building Research Establishment and New Zealand has BRANZ. Nothing much useful has come out of the CSIRO since their datasheet on Foundations. Australia’s best publications have been the Guide to Standards and Tolerances (not based upon any published research) and the Building Code Board’s Durability in Buildings (a wordy but authoritative document).
Ironically if fewer things are going wrong the pariahs and crows have less to prey on. For instance, if we quickly find out that some materials don’t work we can avoid using them and therefore avoid having an unnecessary fight with our client. If we are not fighting, no one needs to spend hard won profit on experts and lawyers. And insurance companies will not have to charge such high premiums if the 75% of avoidable stuff ups are not occurring in the first place.
Solutions mean starting from scratch
If a builder stands around looking, nothing gets done. So we need to fix these important back-end problems or they will keep costing us money and time. We need a road map for an easy to find and use formula on how to deliver good buildings.
I am proposing simple solutions in a series of stages – but this needs to come from the Australian Building Codes Board because this organisation is intelligent and Australia-wide. They are just stuck with things that were unintentionally wrong to start with and have ‘bureaucratised’ the problem because it has become so hard to fix without starting from scratch.
Anatomy of Building
I propose a set of clear details that explain best current building practice. Each detail (see example) would provide a consistent starting point for designers, contractors, engineers, tradesmen and manufacturers to use. Terminology would be the same. No more Australian Window Association detailing waterproofing differently to the non-existent waterproofing rules coming from engineers and manufacturers. Or Standards Australia termite management detail being inconsistent with the requirements of the Premises Code.
The details would unashamedly deal with are high risk issues. Some people have said we cannot afford to build better – I disagree. I have seen so many good builders get punished by small faults caused by a subbie or consultant not knowing what to do. End caps to subsills are the classic example. Or doglegs in valleys. Or timber-framed rooflights.
Help doesn’t need to stop at the detail. I propose that each item in the detail can be electronically addressable so you can also find out any rules and warning, different options of materials to choose, thermal or environmental info, what the relevant Australian Standard requires, any technical info you need such as incompatibility with other materials, and where to find help.
In the end, this is providing a similar framework of knowledge for our industry to what the medical industry calls ‘anatomy’. This is overdue, possible but will take work and teamwork to get it done. How can you contribute to get this done?
Please email me any thoughts or experiences at jwtyrrell@tyrrells.com
Jerry Tyrrell is founder of the Institute of Building Consultants and co-founder of Tyrrells Property Inspections. He has more than 39 years’ experience as a labourer, tradesman, contractor, architect, mediator, building consultant and author. He chaired the Timber Pest Standard and was a committee member of the Termite Management Standard.
Next Issue: Principles of modern lighting