Waterproofing – joint sealants to connect or to release?
Since the introduction of liquid applied membranes, joint sealants have been used as backing material, in a variety of forms. When applied correctly, they offer a fuss-free solution. If used incorrectly, they can cause all sorts of problems. Andrew Gollé explains.
Correct application of joint sealants maximises the intended performance of the membrane material; however, the misapplication of joint sealant materials breaches Australian Standards and material manufacturer requirements, and can result in membrane failure and expensive rectification costs.
Two Types of Sealant Function
Substrate preparation sealants, in waterproofing, are selected according to specific performance requirements of the sealant connection. Two specific requirements are encountered in most waterproofing applications:
To join two materials, forming a bond with the membrane, or;
Allow the membrane to release from junctions where movement can tear the membrane.
Connector sealants are compatible with the membrane material, where adhesion is required onto the sealant. These are typically paintable polyurethanes or Modified Silicones (MS). These sealants connect the membrane, over substrate materials to other termination materials, forming a bonded connection. Examples are membrane connection to barrier stop angles; drainage control flanges; periphery barrier to bath and shower tray edge; and balcony post fixings.
The second type of sealants are used as bond breaker materials. Bond breakers are required by AS 3740-2010 Waterproofing of Domestic Wet Areas. Bonded membranes are required to have bond breakers installed at all floor/wall, hob/wall, and junctions where movement might be expected. Polyurethane sealants are not bond breakers, where they do not allow the membrane to release when subjected to movement. These are termed as fillet joints, and therefore do not comply with AS3740 3.13.7 requirements. Neutral cure silicone, non-paintable polyurethanes or vinyl tapes are used as bond breaker materials.
Connector Sealants
Connector sealants are prescribed under AS3740-2010 3.9 Junctions. Junction flashings are used to connect two types of materials. The practical use applies where the termination of the membrane, over the sealant and onto the receiving material is not possible. For example, a Type 4 junction flashing may be used to connect water resistant concrete floor substrate to non-water resistant timber door jamb and stop. Polyurethane sealant is applied to the concrete floor and timber door frame, allowing connection onto the sealant, and not the timber. Exposed membrane material above FFL, onto the timber door frame is unsightly.
Type 1 to 4 Junction Flashings are the correct application of polyurethane, as a connector sealant. The intention is to adhere the membrane to various materials where bond breaker release can cause membrane system failure. Membrane connection is critical in high use areas, such as wall sheeting to pre-formed shower bases.
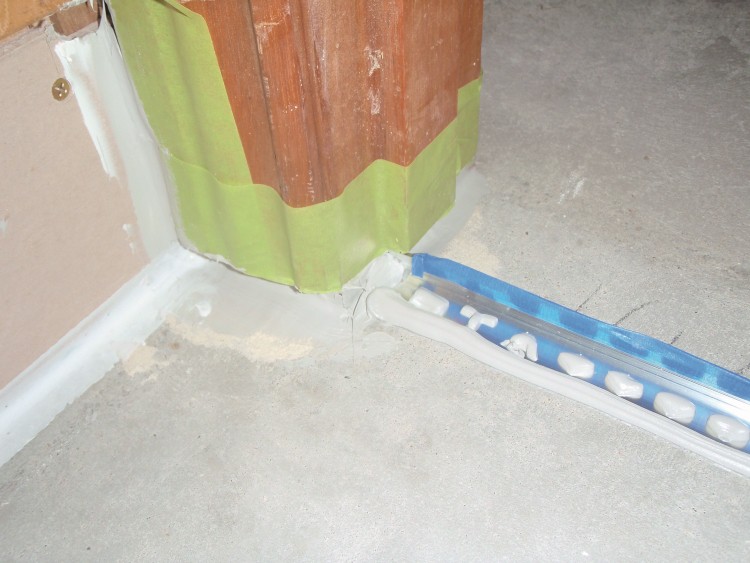
Sealant selection- Type 2 junction polyurethane FC connecting to door barrier stop, Type 4 junction polyurethane FC connecting to timber door frame, Bond breaker neutral cure silicone at wall/ floor junction.
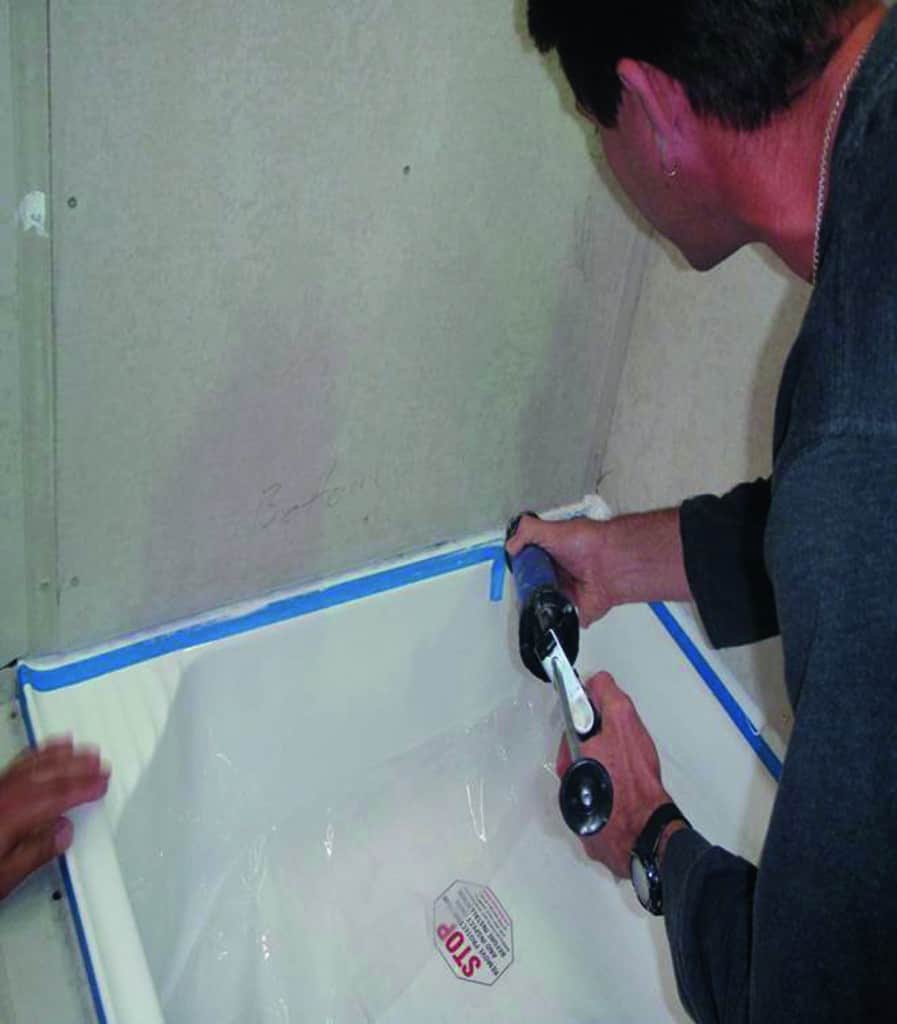
Connector sealant to bath.
Connection to tap combination, mixers and rose penetrations also rely on Type 2 Junction Flashings where membrane contact onto tap spindles may breach AS 3740 3.10.1. Application of sealants to tap penetrations must allow for servicing of the taps without breaking the sealant.
Fast Cure (FC) polyurethane sealants are used in preference to standard cure polyurethanes. FC poly’s are formulated with very low solvent content and gas emissions. Standard polyurethane sealants cure very slowly and continue to release solvents over extended periods. Solvent release from sealants can adversely affect water based membranes. FC polyurethane sealants will moisture cure at a rate of between 2 to 3mm over 24hours, dependent on favourable ambient conditions. Optimum membrane connection is achieved at full cure, and where sealants have completely skinned.
Application of membranes to polyurethane sealants that are still tacky, may reduce adhesion of the membrane to the sealant. This should never be relied upon as a form of bond breaker, as partial bond is still formed, and the sealant may still be releasing residual solvents which may degrade the membrane.
Modified Silicones (MS), silyl-modified polyether, are another type of connector sealant. MS sealants are formulated for specific uses. MS used in waterproofing applications deliver the best of silicone properties and acrylic properties. MS sealants in these applications, are neutral cure and atmospheric moisture cure. They cure as quickly as FC polyurethanes, are paintable, and have good adhesion. They are solvent free and do not bubble during cure. Benefits over polyurethane include water clean-up, low temperature gunability and a skin time of 15 to 20 minutes. MS sealants are used as a Type 3 Junction Flashing when sealing between wall and ceiling linings with shadow line tiling, and as a Type 2 Junction Flashing connecting window reveals to window frames and ceiling mounted rain head penetrations. Some MS sealants; however, have an active window of only 48 hours, where painting with primers or membranes must be carried out within this timeframe.
Bond Breakers
Bond breakers are required by AS3740 3.13.7. Their type must match the movement class of the membrane. Bond breakers are essential, in order to maximise the elongation potential of the membrane. Where a Class 3 membrane ( 300% plus elongation ) is bonded to a polyurethane connector sealant, 1mm of membrane can only stretch to just over 3mm before break. Membrane release off of 12mm of neutral cure silicone can potentially stretch to 36mm + before break. Now, if you have 36mm plus of movement, in your building, you’ve got bigger issues, however you get the idea. It’s about maximising the potential tolerance to movement that the membrane system can deal with. I am sure you will agree that there is a big difference between 3mm and 36mm. Therefore, again, stop using poly sealants as bond breakers!
Class 1 membranes, with an elongation of 0 to 60% require a Class 1 bond breaker over 75mm, with compressible foam backing rod and membrane release tape. Type 1 are used with inflexible membranes, such as polyester resin fibre glass.
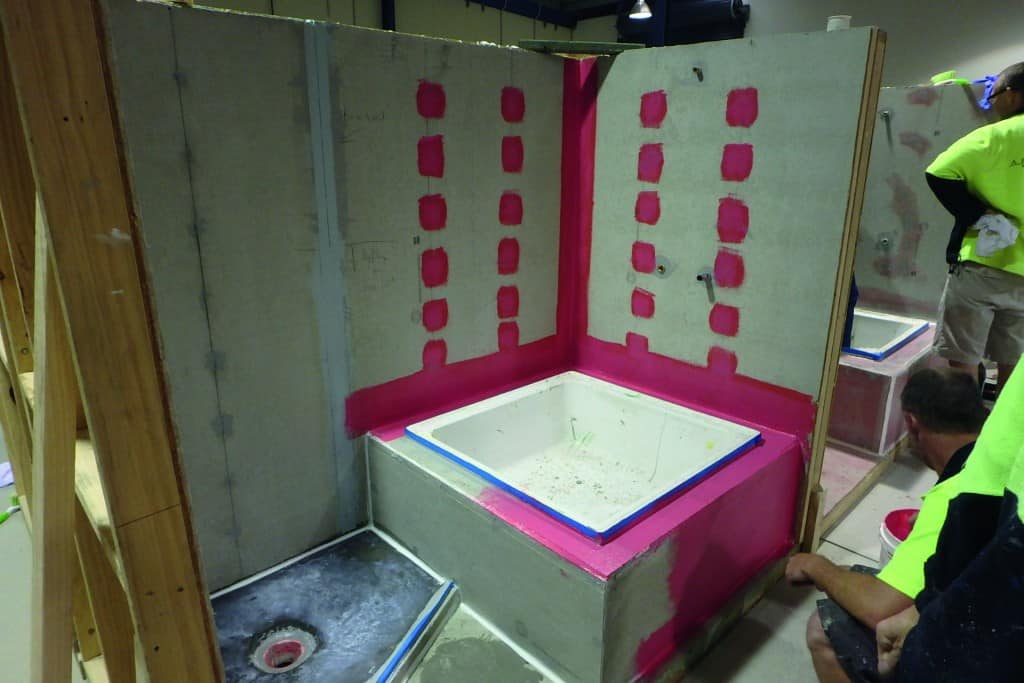
Polyurethane FC connector sealant to bath edge, taps & rose, shower angle, drainage flange and supported sheet joint. Neutral silicone bond breaker to internal corner, shelf corners, wall/ floor junctions.
Class 2 membranes have an elongation of between 60% and 300%. Typically acrylics or cementitious acrylics with an average elongation of 100% at break. These require a Class 2 bond breaker over 35mm which would normally be a release tape or neutral cure silicone. Class 3 membranes will elongate to over 300%. Most water based polyurethanes, latexes and Styrene Butadiene Rubber (SBR) membranes will elongate to approximately 350% at break. Class 3 membranes require a Type 3 bond breaker over 12mm. This will typically be 12mm of neutral cure silicone, or can be bandage as designed by the manufacturer for their membrane system.
These bandages can be polyester, vinyl, latex or neoprene and are intended to release from the substrate and either match the elongation properties of the membrane, or allow the membrane to release and move independently. This is especially relevant on decks sheet joints, where deflection and differential movements result in forces akin to tearing at the membrane like trying to tear a sheet of paper. The appropriate bandage will allow the membrane to release from the substrate and to “Ripple and not Rip”. Bandage must never be installed with membranes unless required by the manufacturer. Introduction of bandage into Class 3 membranes may reduce the membrane back to an inflexible Class 1, and void any manufacturer’s warranties.
Type 1 and 2 bond breakers are best suited where the membrane is applied below the mortar screed; however, compacting the screed directly onto the membrane can restrict the function of elongation as the membrane tries to release from the bond breaker. Bond breaker systems can be optimized by installing foam backing rod in the junctions, on top of the cured membrane, before laying the screed. This allows membrane release from the bond breaker, into a compressible medium.
Type 3 bond breakers are effective where membrane application occurs either below, or on top of the screed. Where membrane application is below the screed, consideration should be given to installation of foam backing rod, on top of the membrane to optimize bond breaker function.
Type 3 bond breakers, with Class 3 membranes above the screed are the most effective. The 12mm span of bond breaker at movement junctions is effective where the membrane is not locked in as tiling is kept 3 to 5mm clear of abutting substrates. Tile thickness and flexible tile adhesive allow for a functional 12mm range of membrane release area.
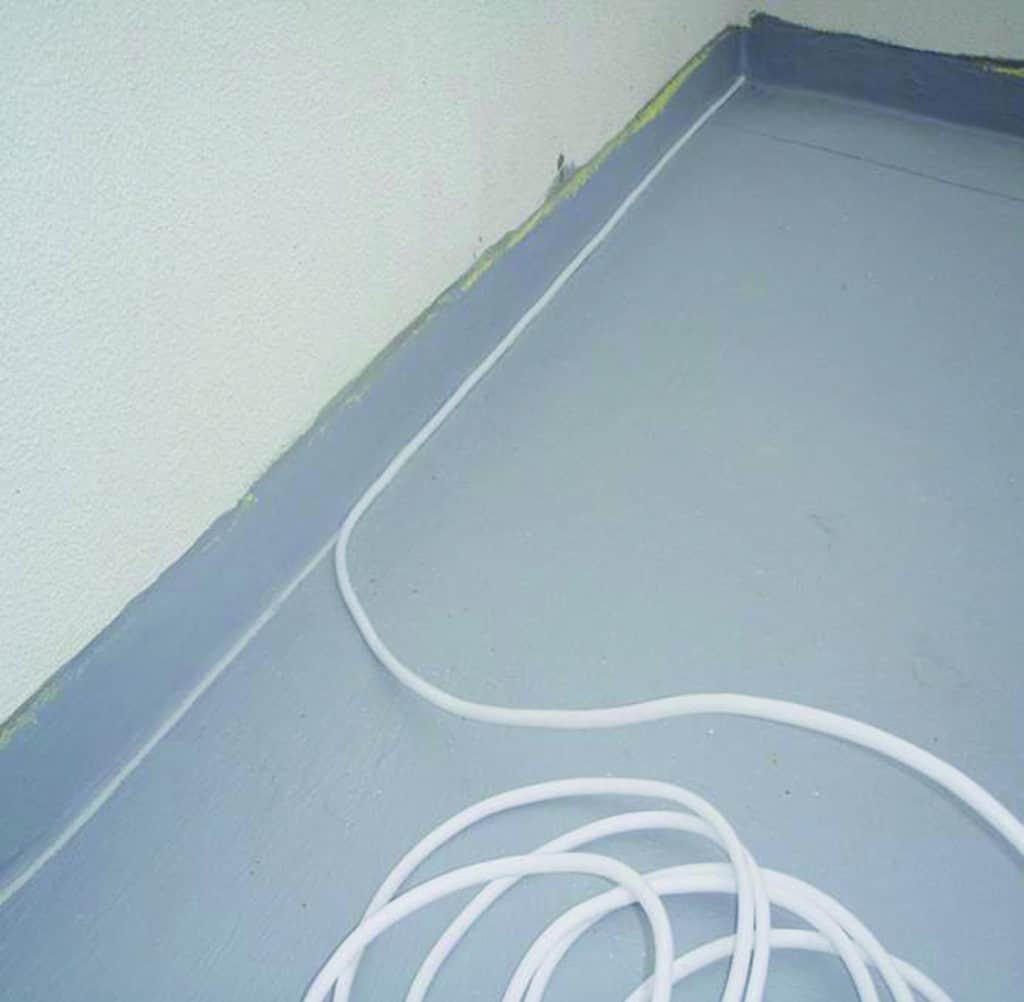
Backing rod installed over membrane as bond breaker release medium.
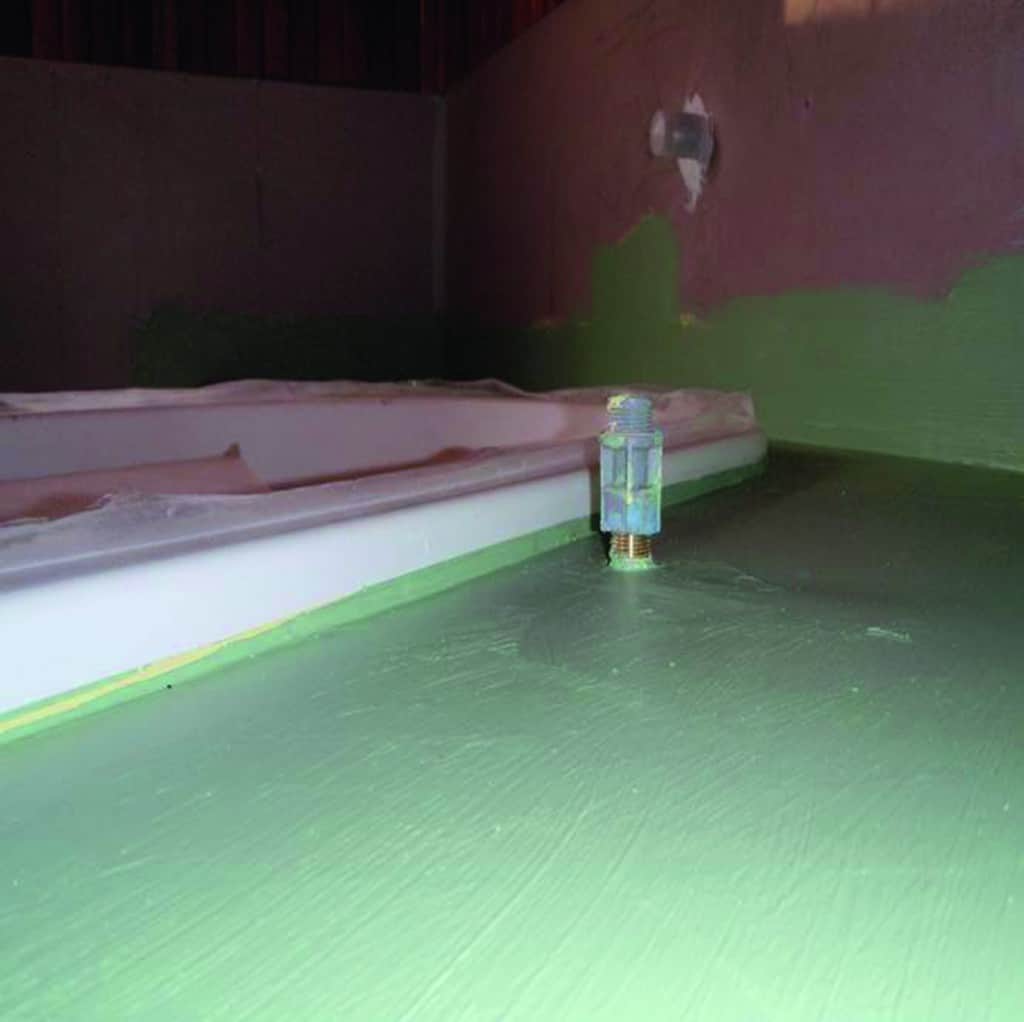
Membrane dressed to Type 2 connector sealant as spa periphery barrier.
The Final Word
Sealants in waterproofing must be selected according to their use as either connector sealants or bond breakers. One sealant type will not serve both functions effectively. As connector sealants are generally paintable and compatible with membrane materials, they must be installed first. Bond breaker sealants are installed next.
This is critical to maintaining integrity of the membrane, especially where bonded barrier stop angles meet wall/floor movement release joints. The rule of thumb is: “Connector before Breaker”, as polyurethane will not stick to silicone.
Manufacturer’s recommendations should be followed at all times. If in doubt, site specifications and stage inspections should be sought from the manufacturer.
And try not to get it in your hair!