Lightweight construction on the rise
For a few reasons, multi-residential timber framed construction’s an increasingly popular option in Australia. Kevin Ezard explains why, and where it could be going.
The party wall feature for this issue demonstrates the spectacular success of Multi-Residential Timber Framed Construction (MRTFC) launched by the Australian timber industry in the mid-90s, which has now become the ‘normal’ way to build multiple dwellings.
Initially the concept was to offer builders a more efficient system than the traditional masonry and concrete internal separating walls requiring wet trades, using timber framing that enabled carpenters to work continuously for improved workflow and fewer delays.
Benefits derived from this approach by builders included faster construction from the elimination of one trade, improved job scheduling and lower costs, reduced interest payments and quicker property turnover. Combined, this provided adequate incentive for builders to change their building methods.
The MRTFC system basically involves the use of fire and sound-rated timber framed wall and floor systems to provide for vertical and horizontal separation between dwellings. It was introduced into the BCA following extensive testing – particularly with regards to fire ratings and studies of life safety.
Over the ensuing years, the timber industry has continued extensive research into and development of the timber framing system to improve fire and acoustic performance. This in turn has also lead to the development of associated building materials – including plasterboard and wall cladding – to further enhance system performance and construction methods.
Taller storeys
The use of MRTFC has largely been in the housing sector (Class 1 buildings) where timber is the most efficient and economic building material for construction, however the multi-residential and commercial Class 2 and 9 building sector is now taking a greater interest in lightweight timber construction.
This trend is a result of an increase in the density of dwellings required in the middle and inner suburbs, which itself is due to the conversion of industrial land and infill projects surrounding city centres as a strategy to contain population growth in most Australian cities.
These medium density property developments are subject to high land costs, and they typically need to be three or more levels high to be economically viable for the developer.
A number of developers are building up to five storeys or higher, and they confirm that lightweight construction with prefabricated timber framing is the answer for fast construction, offering savings of 25% or more over traditional materials – particularly on difficult sites where they can minimise crane or scaffold use.
There is, however, a barrier to the greater use of timber: the Australian Building Code currently only allows up to three storeys for timber frame construction. Internationally this is generally much higher for timber buildings, either with or without sprinklers.
A submission to the ABCB is currently being prepared, which seeks permission for the NCC-BCA to increase the allowable building height to 25m for the construction of timber buildings up to eight storeys high utilising DtS solutions.
If it’s accepted, this change would significantly reduce current regulatory requirements, lower the costs of engineering and documentation, and improve productivity through the prefabricated construction of lightweight multi-residential buildings.
The timber industry is well positioned for the increase in demand this would bring, as the timber framing and components required for building up to eight storeys is much the same as it is for domestic construction of 2 storeys, and current carpentry and building trades would be required for prefabrication and site installation.
New materials for a new era
Building materials manufacturers currently supplying the residential and commercial markets have also been making significant progress developing technology for improved products that are part of lightweight construction systems.
An excellent example is the ongoing developments in plasterboard, with the Partiwall® system by USG Boral – essentially a twin-wall system incorporating fire-resistant plasterboard panels within the wall cavity – installed during the framing stage, followed by internal wall linings at the plastering stage.
In conventional fire-rated wall systems, fire resistant outer linings provide protection to the wall substrate; however with the Partiwall® system, the main fire barrier is located within the wall cavity and is designed to protect the structure on the side opposite to the fire.
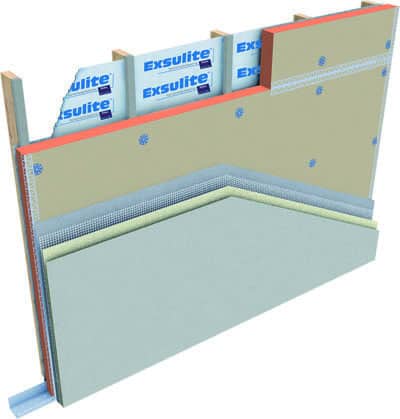
A cross-section of the lightweight Exsulite façade system.
Another example is a recently developed façade used in ‘The Green’ residential apartment complex by Australand in Parkville, Melbourne. The Green is a five-storey building constructed using lightweight timber frame construction, which featuring numerous new-generation building systems all interlinked to provide a faster and more efficient construction process.
The new Exsulite®-Kooltherm® Thermal Façade System, a rigid cladding system with a high performance thermoset insulation core, was use for the external walls. This was fixed to the timber framing with battens secured on-site and coated with the Dulux® AcraTex® weatherproof coating system.
Developed jointly by Kingspan Insulation and Dulux® AcraTex®, this new product has high performance insulation characteristics, lightweight rigidity, and outstanding thermal efficiency.
There are a host of good reasons for building using lightweight timber construction, one of which is achieving more affordable housing. And with the significant reduction in the cost of building timber framed medium density dwellings, we’re going in the right direction.
For more on this topic, ‘Building with engineered wood construction systems’ is the theme for the Frame Australia 2015 Conference and Exhibition, to be held in Melbourne on 1st June.
Visit the website for more details: www.frameaustralia.com