Alternative solutions for wet areas: if it leaks, it fails
While alternative solutions are now acceptable in building projects, you must ensure that the one you choose, or are provided with, actually complies with legislative requirements. Andrew Golle explains.
Wet area defects represent approximately 73% of building defects nationally and regardless of the licensing regime, or statutory inspections, wet area failure is fairly consistent throughout all states and territories. The main reasons for this consistent failure rate are:
Too many cooks: concreters, carpenters, block layers, plumbers and plasterers can adversely affect substrate preparation of the wet area before the waterproofer has to deal with it. Tile layers, vinyl layers, glaziers and fit off crews then go about drilling holes through treated areas, thereby compromising the waterproofing system.
Lack of supervision: project managers, builders and site supervisors overlook breaches throughout the construction chain and push forward towards the finishing trades covering up any hidden defects.
Misapplication of products: compatibility chains are not followed, paint on membranes is applied at sub-standard film thickness and then mechanically abraded by unbonded screeds and finish materials. Builders rely on the specialist knowledge of their waterproofers and others in the construction chain. Refer to point 1.
Ignorance of BCA requirements and Australian Standards: localised practices take precedence, sometimes enabled by ignorant building surveyors, certifiers and council inspectors. I have been made aware of a practice recently, where, local authorities are knocking back barrier stop installations at wet area doorways if the angle does not protrude at least 3mm above finished floor levels. The justification being that surface water will bead up to 3mm through surface tension. This has popped up in Cairns, Dubbo and Hobart. This practice provides a trip hazard, breaches lippage requirements under AS 3958.1-2007 Guide to the Installation of Ceramic Tiles and breaches AS 3740-2010 Waterproofing of Domestic Wet Areas where barrier stop angles are to finish flush with floor level openings. Please stop it, whoever you are.
BCA (NCC) COMPLIANCE
In order to address these ongoing defects and to provide a consistent standard of building, all states and territories have legislated to adopt the National Construction Code (NCC) as the mandatory minimum standard of building and construction. The next update to the NCC will be adopted on 1 May 2016 under state and territory legislation, thereby superseding previous editions. This is due to developments in new practices which are assessed and adopted by the NCC where they comply with the performance provisions.
The NCC requires that a building solution complies with the performance requirements. This can be achieved by either:
Complying with the deemed to satisfy provisions. Part 3.8.1 of NCC Volume 2, references AS 3740-2010 as the deemed to satisfy solution.
An alternative solution as determined by NCC 1.0.8, 1.0.9 and 1.0.10. I won’t go into the requirements as these have been covered by previous articles in this publication.
An expert judgement following the verification methods prescribed and documenting evidence of suitability under Part 1.2.
A combination of above where these do not adversely affect the performance provisions of other building elements.
However, the performance provisions are the premium factor that all building solutions must lead back to and comply with.
Under NCC Vol 2 Part 2.4.1, the performance provisions are:
To protect the structure of the building and to maintain the amenity of the occupants, water must be prevented from penetrating:
behind fittings and linings
into concealed spaces of sanitary facilities, bathrooms, laundries and the like
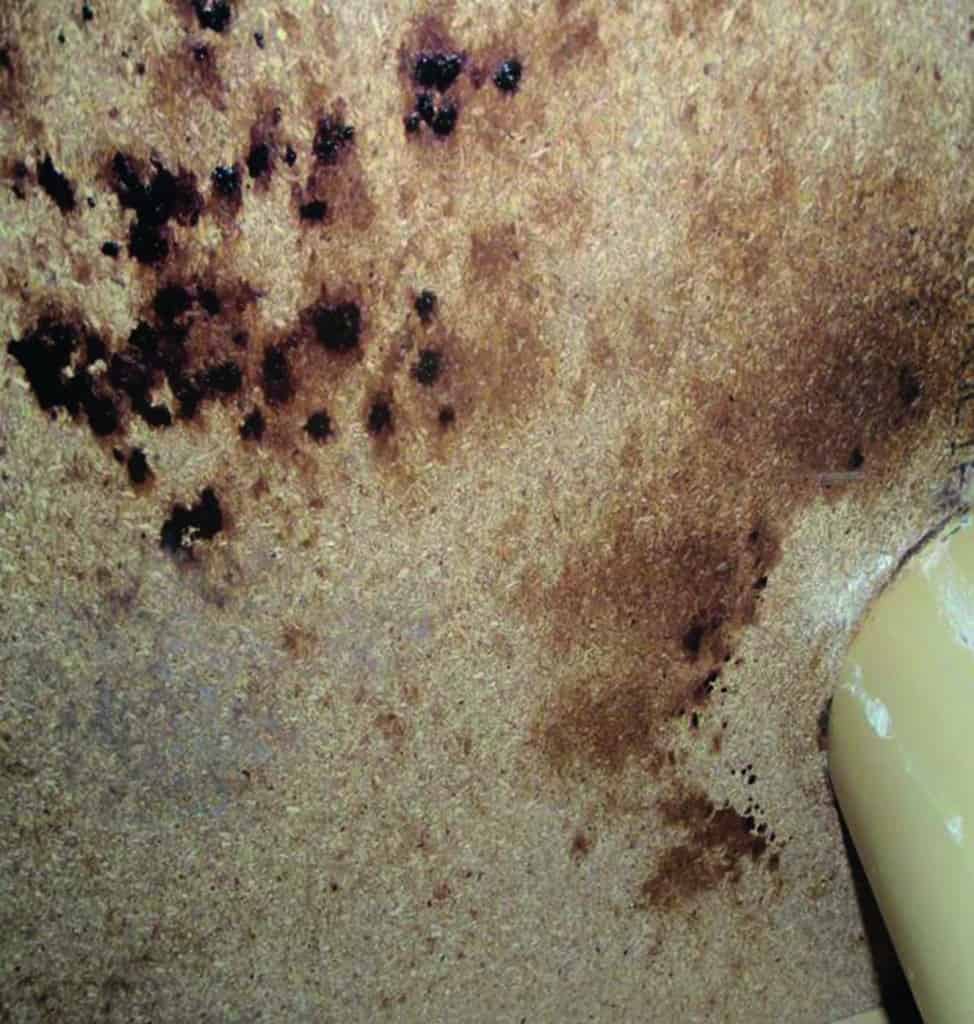
The effects of water damage to particle board flooring can be quite devastating.
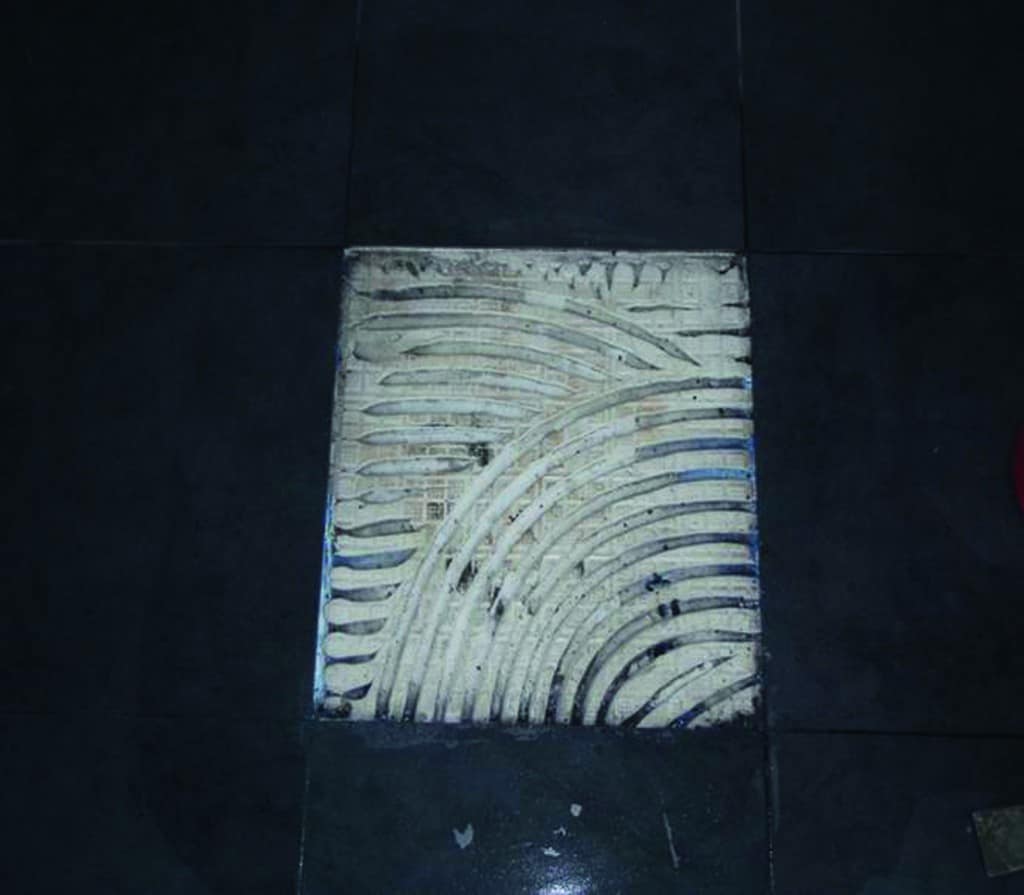
Contact coverage.
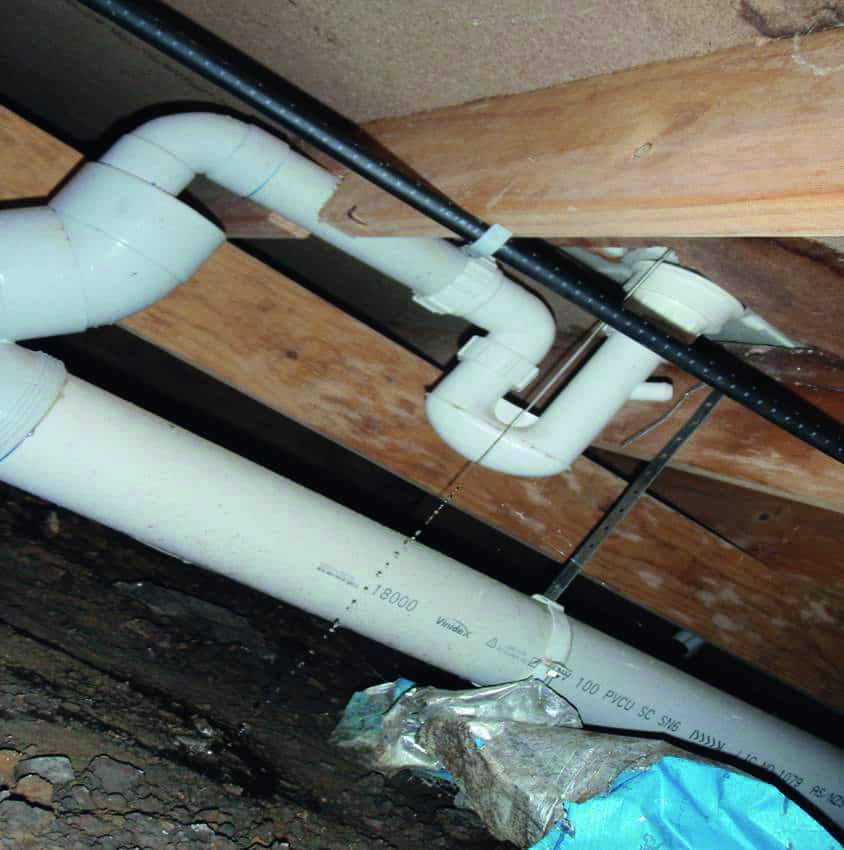
Once particle board flooring is exposed to copious amounts of water damage, there is no other option than to rip it out and start again.
AN ALTERNATIVE SOLUTION – WILL IT LEAK?
It is up to the building surveyor/certifier/local authority to assess and accept a building solution as one which will comply with the performance provisions. Will it leak, rot stuff out, cause it to fail or adversely affect the health and amenity of the occupants? The deemed to satisfy referenced construction manual, which in most cases is the NCC referenced Australian Standard relevant to the construction, is assessed as being compliant. AS 3740-2010 is the document, in this case.
Where an alternative solution is provided, the appointed certifier must independently read and assess the documentary evidence provided as being compliant with the performance provisions.
The following are extracts from an alternative solution, prepared and signed by a professional engineer and accepted by local authorities. Please appreciate that the entire report has not been reproduced for your perusal, and we have only taken out the relevant excerpts.
The entirety of the alternative solution is to justify the exclusion of waterproofing application to particle board flooring substrate to wet areas outside of the shower enclosure.
The reasons for the provision of an alternative solution is that the construction practice of non-treatment to particle board flooring is no longer recognised as a deemed to satisfy solution by the NCC. The report writer states that non-treatment of the particle board outside the shower recess is in accordance with traditional Victorian building practices that were recognised by Victorian Government legislation from BCA 1996 through to BCA 2003. It is argued that this has been a legally recognised construction practice for over 20 years, where more than 300,000 homes have been constructed using this system.
It is stated that changes to the Standard, requiring full coverage waterproofing to particle board flooring, were due to national issues originating in NSW, where poor workmanship practices have led to a number of defective wet area installations.
He states that the Victorian Building Commission has not issued any direction that wet areas are a major problem and that remedial work is required.
The above statements are completely false. Victoria has just as many wet area defects as the rest of the country. A major cause is the non-treatment of particle board outside of the shower enclosure.
Secondly, the report writer states after much justification, that internal grade particle board does not require treatment by a waterproofing membrane as the material is classified as a water resistant substrate under AS 3740 Clause 2.4.2 (b). The Standard defines that a concrete floor substrate is also deemed to be water resistant under the same clause. He therefore concludes that a water resistant timber floor will achieve the same level of performance as a water resistant concrete floor.
The Standard defines that water resistance is where the property of a material restricts moisture movement and will not degrade under conditions of moisture. Bathrooms, W/Cs and laundries are classified as wet areas requiring water resistance to floors.
He fails to include in his report that AS 3740 Table C1 requires full waterproofing treatment to timber floor substrates in areas adjacent to baths and spas – this means outside of the enclosed shower where otherwise concrete and F/C sheeting are deemed to be sufficient as water resistant. The Standard also states that timber flooring substrates be installed in accordance with manufacturer’s requirements. Manufacturers of timber flooring products state that their products are suitable for use in internal wet areas such as bathrooms, toilets and laundries where covered by an impervious material: a waterproof membrane.
This justification is therefore flawed.
Next, the report writer justifies that it has been common practice in Victoria to install the floor tiling adjacent to enclosed showers with a waterproof tile adhesive. If a waterproof tile adhesive is applied with a notched trowel, then this would be sufficient to provide a water resistant sealant across the top of the particle board flooring.
This argument is not correct, as waterproof adhesives are not used in general practice, where the adhesive material qualities and application methods are not sufficient to provide an impervious cover, as required by the timber flooring manufacturer. Suitable tile adhesives that will not degrade under contact with moisture are mostly porous, either due to cementitious materials, crumb fillers or air cavities. AS 3958.1 requires 90% adhesive contact coverage for wet area tiling installations. This still allows 10% air cavities, holding free standing water in porous adhesive, grout and tile strata, which in turn make contact with particle board substrate. AS 3740 Part 2.4 requires that water resistant lining materials comply when used in conjunction with compliant substrate materials. We can’t use one without the other; we must use compliant lining and substrate materials in combination.
The above reasoning is therefore flawed.
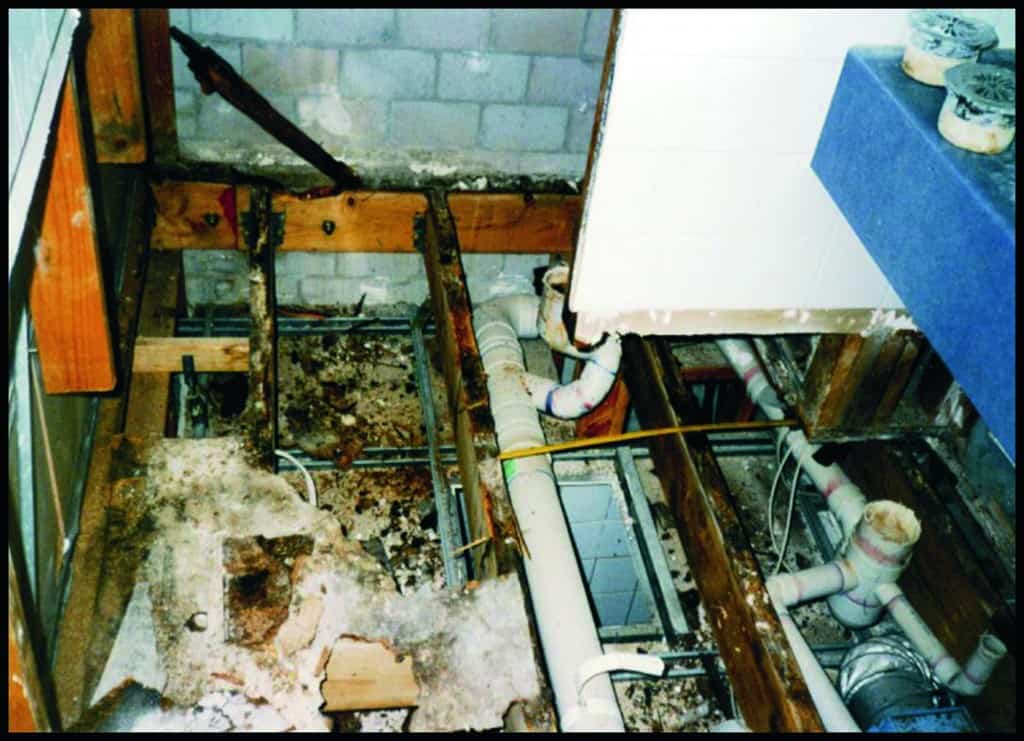
A sure sign of a tray leak from beneath the floor.
WHAT DOES IT ALL MEAN?
At the end of the day, State and Territory legislations require compliance with a National Construction Code in order to provide a minimum standard of building and provide protection to the building owner. The NCC requires that we comply with the performance provisions. We must construct the wet areas to restrict water movement out of the area, stop damage to other building elements, and maintain the health and amenity of the occupants. The above alternative solution is not a building solution but a cop out that attempts to excuse the applicant from complying with NCC.
It falls onto the shoulders of the surveyor/certifier /council inspector to read and assess the alternative solution.
As builders, we therefore try and reduce the risk of performance failure by utilising the Deemed to Satisfy Provisions, as a minimum, and then to adopt best practice to ensure functional performance. For example, even though a kitchen is not scheduled as a wet area, under the NCC, we know that there are water services in place and the potential for damage to sensitive building elements or to allow water to enter wall cavities. In order to satisfy performance provisions, we seal the bench top to the wall lining, waterproof the sink splashback and dishwasher recess, and seal all service penetrations. We seal toilet stop cock penetrations over 25mm above FFL. We seal tap penetrations over 150mm above the bath splash back. We waterproof the full floor area, regardless.
As a builder, you must also read and assess any design directions or alternative solutions provided to you. Do they actually comply with your legislative requirements and performance provisions? Are you putting yourself at risk by following these directions, even though they are issued by professional designers and engineers, and given the nod by your certifier?