Luyten: Up to 30% of Australia’s remote areas could be built with 3D printing
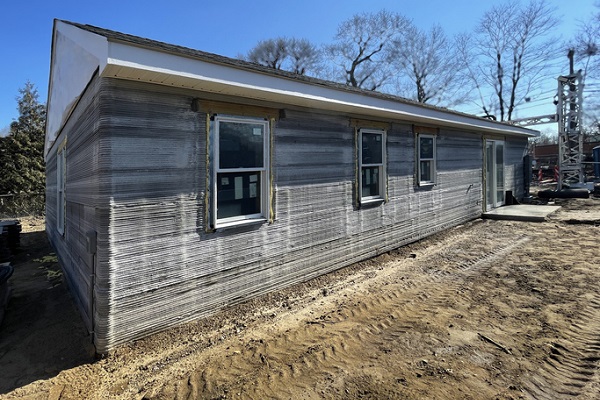
Exterior side wall of a 3D printed house under construction for sale to the public. The roof and windows were done with traditional methods.
Up to 30% of Australia’s outback, regional and remote areas could be built with 3D printing technology by the year 2030 according to Luyten co-founder and chief executive, Ahmed Mahlil.
Luyten is an Australian 3D printing building and construction company. Ahmed says that the trend toward 3D-printed construction is already underway across the world.
“In 2016 the United Arab Emirates became the first country in the world to promote 3D printing in its construction industry, setting a 25% target by 2030. Other countries are following suit,” he says.
The commitment to 3D printing has reduced construction waste almost tenfold and reduced CO2 emissions by up to 70%. It has also reduced transportation emissions when building in remote areas by as much as two tons per home demonstrating its capacity to solve the rural housing deficit.
USA president, Joe Biden, has launched the America Makes Forward program, designed to further spur the growth of additive manufacturing in the country. The program will see the U.S. government and giant multinationals support 3D printing initiatives, small and medium-sized enterprises in various ways.
“While Australia has not yet put in place targets, we are moving quickly to foster a robust and cutting-edge 3D printing industry that will help to solve the housing affordability crisis and also assist our nation in building housing and other building structures in remote areas that are impervious to challenging environmental conditions,” Ahmed adds.
He believes that the 30% target may even be exceeded by 2030 to 50% as it is very clear now that 3D printing is not a trend. It is a technology that has been maturing for 30 years and different sectors are already reaping the rewards.
“What many people do not realise is that the 3D printing of homes and other buildings is already underway in Australia. In fact, we are building the first 3D indigenous housing project in the world,” Ahmed says.
“The project is being undertaken in Australia’s Northern Territory and involves the build of several houses using Luyten’s cutting-edge 3D building and construction printing technology.
“Australia’s red centre consists of some of the harshest weather on the globe. Temperatures often range from -5°C in winter and close to 50° in summer and there is little shade. The land is extremely arid and not ideal for conventional housing. Not only is it difficult to get traditional construction materials out there but the cost is also prohibitive.”
Luyten as a company believes that 3D printing in Australia is about the revolutionise the building sector.
“The technology is proven to increase construction site efficiency with 60% guaranteed costs savings, 300 to 500 times shorter execution times, and an 80% total reduction in monetary expenses without formwork in concrete construction,” Ahmed says.
“We are acutely aware of the construction industry’s carbon footprint and determined to create construction solutions for generations to come that reduce emissions. Our unmatched technology employs up to 40% less carbon dioxide emissions through propriety mixes that reduce use of cement, and the robotic systems reduce construction site and logistics carbon dioxide footprints by 50 to 70%.”
Luyten 3D’s printed houses are Australia and New Zealand building code (AS/NSZ 1170 and AS 3600) compliant and are built using Luyten’s highly robust and eco-friendly Luyten Ultimatecrete 3D printable concrete which results in 82.5MPa compressive strength after 28 days, four times stronger than the 20MPa residential building code requires.