The barrier to corrosion
It’s been on the market for a few months now, but if you’re one of those who has heard of next generation Zincalume steel and are still wondering what the fuss is all about, then we have the answers for you: what’s different about it and most importantly, why you should care.
There’s a pretty good chance you have already come across BlueScope’s promotion for its next generation Zincalume (AM125) product, which hit the market in August this year.
It’s a name that the building industry is already familiar with, given that original Zincalume steel (AZ150) made its market debut in 1976. It was then given a slight makeover 18 years later with the addition of a resin coating to improve mark resistance.
Let’s be honest though. A lot of you are probably sceptical about this new offering and how it differs from its predecessor. With the seemingly endless number of new technologies and products that are being dubbed as ‘innovative’ (the leading buzzword of the day), it does get to the stage where you wonder if all the spin is genuine, or simply, spin.
However, the brains behind next generation Zincalume steel argue that it is more durable, more efficient and more sustainable than its predecessor – BlueScope also has 17 years of accelerated lab testing and real life outdoor exposure to back up these claims.
“Zincalume steel has been in our market since the 1970s. It’s been the benchmark performing product for that time period and we don’t take tinkering with it lightly,” BlueScope market manager (commercial and industrial) Manu Siitonen says.
Manufactured under a range of Australian and international patents, BlueScope has invested more than $100 million to develop its next generation coating and the associated manufacturing technology.
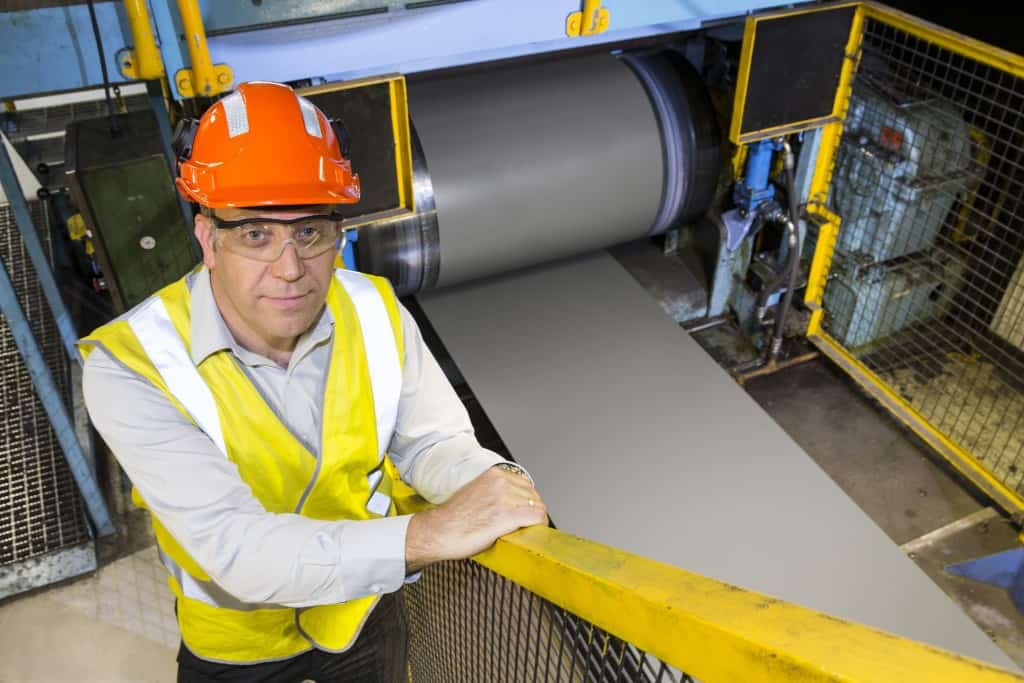
BlueScope market manager (commercial and industrial) Manu Siitonen.
“Our improved Zincalume steel represents an enormous investment of time, manpower and money by BlueScope in developing a product that provides significant durability advantages over other steel building products,” he says.
Manu credits the inclusion of a protective coating – known as Activate technology – as the key to ensuring that the next generation of Zincalume has a more effective corrosion resistance.
Activate technology for dummies
So what exactly is Activate technology and why is it so special?
It basically extends on Zincalume’s existing protective alloy coating of zinc and aluminium, which protects the steel against corrosion. The next generation product introduces magnesium into the equation, which improves galvanic protection by activating the aluminium. This forms a unique protective barrier that enhances corrosion resistance and ultimately results in a longer-lasting product.
“The addition of magnesium forms a pinnacle part of the coating,” BlueScope Steel Research product development portfolio leader (polymer coatings) Detlev Mueller explains.
“The enhanced coating is designed to better protect the base metal layer, meaning that exposed surfaces are more resilient when drilled, cut or scratched during construction.
“This modification showed a huge improvement in terms of cutting edge performance as well as performance in terms of corrosion testing, either accelerated or outdoors – to the extent that it allowed us to reduce the cutting mass and still provide a product that is above and beyond what we’re providing now, both in bare and painted form.”
As mentioned earlier, BlueScope certainly put next generation Zincalume steel through its paces in order to ensure its durability and be confident that it could perform to standard.
Testing, testing
While accelerated laboratory testing is useful in a product’s initial phase of development, it really is no substitute for the assurance that comes from many years of field testing.
Over the 17-year period, more than 2000 panels were tested in Q-Fog cyclic testing and salt spray testing in laboratories. A further 3000 panels were tested in 22 different exposure sites in Australia and around the world, including New Zealand, China and the United States.
“The majority of field testing was conducted in Australia to ensure that next generation Zincalume steel could cope with unique local conditions,” Detlev explains.
“Seeing that so much was at stake in changing our flagship product, we really went that next step further. We tested on 50 building sites and manufactured five purpose-built test structures in various locations throughout Australia that aimed to test the technology against different elements – severe and mild marine environments, extensive sunlight, high humidity, strong winds and low air quality. There were also some tested in industrial locations.”
In terms of corrosion performance, the biggest improvement was found in the most severe environments, which also gave BlueScope the opportunity to rethink its manufacturer warranties (see breakout box).
“When we compared the corrosion performance of next generation Zincalume with the original product, we found the biggest improvement in the most severe environments – such as surfaces which were unwashed by rainfall and also subject to air pollution,” Manu says.
He adds that the new product was developed in response to emerging building requirements that demanded improvements in areas such as material efficiency, durability and sustainability.
It’s easy being green
On top of its extended durability and corrosion resistance, next generation Zinclaume also has its benefits in terms of sustainability, which, as you know, is becoming all the more important in the building sector these days. Essentially, the new technology has increased product lifespan while using fewer metal resources.
BlueScope recently completed a comprehensive Life Cycle Assessment (LCA) which covered ISO 14040:2006 methodology, cradle-to-grave environmental impacts as well as third-party peer review. It found a smaller environmental footprint of between 10-25% when compared to previous-generation Zincalume steel, both in commercial and industrial roofing applications. This is because the improved coating enables a more efficient use of natural resources through the reduced use of zinc and aluminium, lessening its environmental impact.
“Just as original Zincalume steel gave builders and architects the ability to realise different designs and construction methods, next generation Zincalume steel has been developed to meet the demands of our changing built environment in regards to durability and sustainability, to inspire those who create for the generations to come,” Manu says.
That’s what we like to hear
BlueScope’s efforts to increase the corrosion performance of its steel through the use of Activate technology has also allowed the manufacturer to offer greater warranty periods for next generation Zincalume steel (AM125).
This is particularly useful for metal roofing projects located close to marine environments.
“If we improve the performance of the product and we’re very confident about its performance, we can provide an extra degree of reassurance to the people buying the product. One of those ways of reassurance is through extended warranties,” BlueScope market manager (commercial and industrial) Manu Siitonen says.
“We want people to be creative in the use of steel and not have to worry about what’s going to happen to the product, their client’s building and ultimately their reputation. You’ve only got one reputation to lose and how we manage our warranties forms a massive part of that.”
The superior corrosion resistance of the next generation product when compared with outgoing Zincalume steel was confirmed by independent testing conducted by the internationally-recognised French Corrosion Institute.
Please note that these warranties are subject to application and eligibility criteria.