The changing state in awareness of building products compliance
By far the biggest issue in the building industry at the moment is the use of non-compliant building products. Gary Smith explains why everyone needs to be more stringent in their approach to choosing suitable product on building projects.
Exploding glass panels, water damaged interiors, wrong sizes, faulty electrical cables, non-conforming wall panelling, fraudulent certificates… we know it started a number of years ago but where will it all end?
The Australian Window Association (AWA) team have taken an average of 170 technical calls a month since the beginning of 2015 and another 20 requests a month for mediation, reports or inspections. That’s about nine a day with a small team of five experts to listen, research and respond amidst myriad other things they undertake on behalf of industry and members. Roughly half of these are from non-members such as certifiers, builders and homeowners and at least two a day are about potential non-conforming products
The CFMEU recently published a submission regarding government procurement procedures, highlighting that the Australian government is a significant influence in the building and construction indu
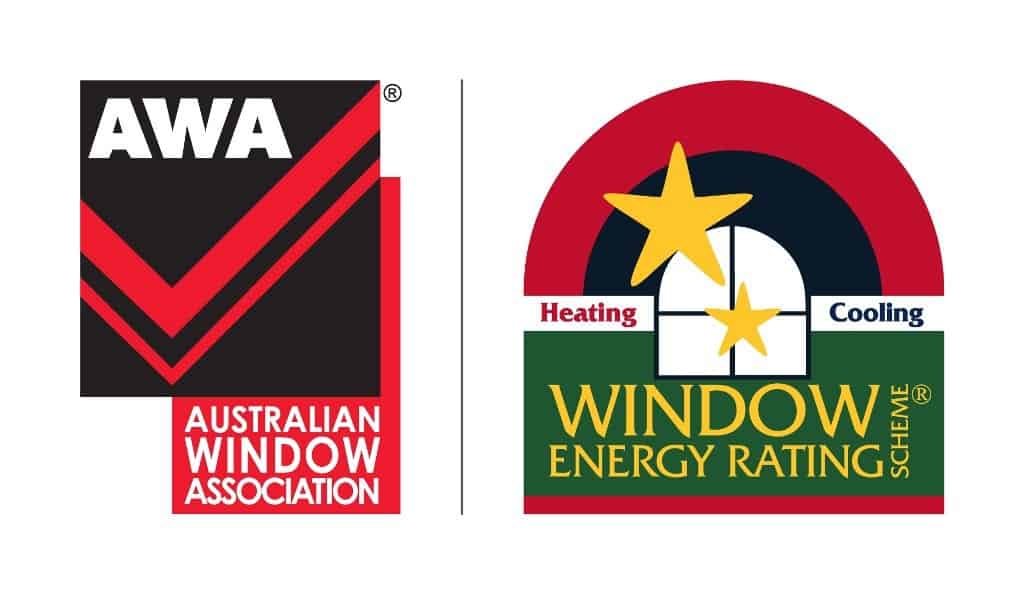
AWA-WERSlogos
stry as an important consumer and funder of projects. In the statement, the CFMEU stated that it (the government) needs to play a leadership role by ensuring that imported, non-conforming, sub-standard building products and furniture are never used in Commonwealth funded and capital supported infrastructure projects. No matter how cheap the product is, if it does not conform to certain critical Australian Standards, it cannot represent value for money.
They stated that the amount of non-conforming imported windows, doors and other glass and aluminium based products including glass curtain walls, balustrades and balconies, aluminium and glass ‘shopfront’ products on the Australian market has reached epidemic proportions. Non-conforming product is most prevalent in the high rise residential and office market as windows and doors for those buildings tend to be consistent dimensions through all the levels, lending this market to high volume importation on a per project basis by builders and import suppliers.
In a further media release on 4 May 2015 following a building fire in Melbourne, the CFMEU called for import restrictions to be slapped on companies found to have manufactured building products that do not comply with Australian Standards.
The AWA has responded to many projects, committees and requests for articles and interviews specific to this issue for our industry at the state, territory and federal levels.
In April, Tracey Gramlick the Executive Director of the AWA was invited to join the QLD MBA at their meeting with Hon Karen Andrews MP, Parliamentary Secretary to the Minister for Industry and Science, to discuss the prevalence of non-conforming products as a major concern for the Queensland building and construction industry. The key concern being for consumer safety and better supporting industry in meeting its obligation to provide buildings that are safe.
All present shared a broad consensus of the urgent need to reform the current system to provide specifiers, purchasers, installers and certifiers with a clear mechanism to determine whether products are fit-for-purpose as defined under the National Construction Code.
More must also be done to remove non-conforming products at the point of sale and to proactively identify and remove from our buildings non-conforming products that slip through the net. Collectively we need to send out a message of ‘not on our watch’.
They pointed out that industry is already doing a lot towards addressing the problem in building an extensive array of third party product certification schemes of varying quality and scope. Some industry associations, such as the AWA, even have accredited inspection and auditing processes. The MBA wrote a letter of thanks and recommendations for the federal government to consider the following immediate steps towards a solution:
Government endorsement and common labelling of existing third party product certification schemes that meet the following minimum requirements:
– accredited through the JAS–ANZ;
– includes product conformity requirements for type or batch (ongoing) testing to Australian or International Standards as – appropriate, as well as a process for ongoing, periodic auditing; and
undertakes market surveillance to identify and weed out fraudulent activity.
On 23 June Independent Senator for South Australia, Nick Xenophon, announced a Senate inquiry into the safety and legality of imported building materials in Australia.
The inquiry, co-sponsored by Senators John Madigan of Victoria and Jacqui Lambie of Tasmania and approved by the Senate, was set up amid rising safety concerns about substandard imported building materials and the lax rules that let them into the country.
High profile incidents have included massive windows falling off the new ASIO headquarters in Canberra and a hi-rise building fire in Melbourne’s Docklands last year that quickly spread when the exterior cladding – imported from China – caught on fire, something that should have been impossible under Australian building regulations.
The inquiry follows consultation between Senators Xenophon, Madigan and Lambie with the Housing Industry Association (HIA) and Australian Windows Association Executive Director Tracey Gramlick, and other representatives of Australian building products makers, which are required to meet strict safety standards.
Senator Xenophon said a key aspect of the inquiry will be the inspection and regulation framework that was clearly failing.
This year’s changes to the AWA independent third party Accreditation Program have been well received by manufacturers and the market surveillance part of the program, including the physical testing of products purchased from the market place, commenced in July. This will underpin a move to address product conformity concerns in windows and doors and has been well received by governments and regulators.
Let’s face it; when a decision is based on price only and fitness for purpose and whole of life costs are not adequately taken into account when procuring window and doors, the impact can be negative on safety of the fabricators, installers, certifiers, consumers and the public and the long term asset value.
There are a few steps you can take to make sure your window and door products meet the requirements of the National Construction Code.
– Ask for copies of Test Reports
– Look for Labels
– Ask for Compliance Certificates
– Check the AWA Website for companies association membership listing
It really is time for buyers to Be Aware.