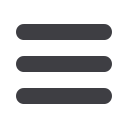
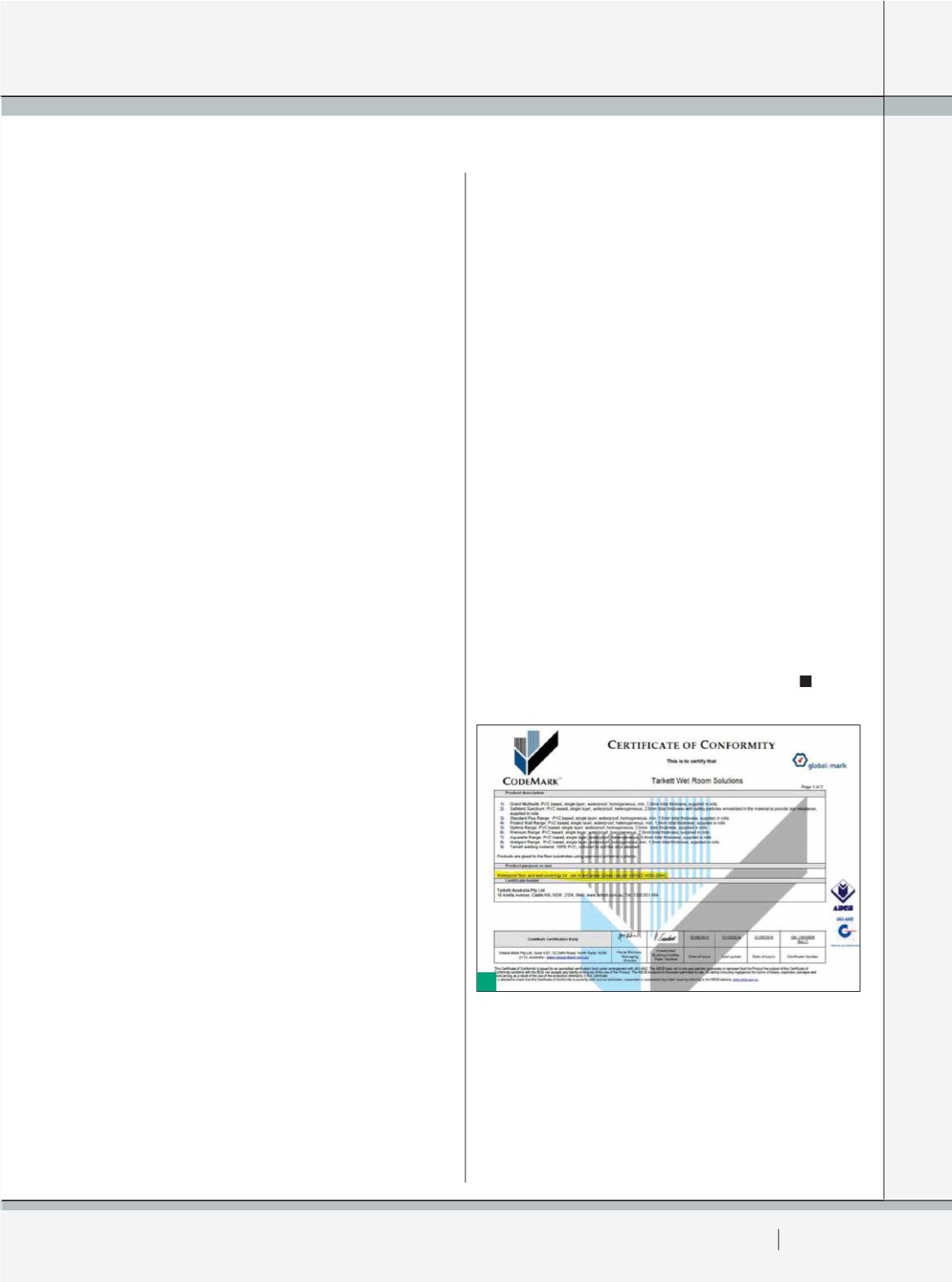
BUILDING CONNECTION
SUMMER 2016 17
will be broken down and compromised by solvent based
adhesives through plasticiser migration out of the
adhesive. This occurs over time and is catalysed by
moisture and heat. What better place to find moisture and
heat than the floor and lower wall areas of a shower.
2. Abrasive damage to membranes by vinyl installers - This
occurs when installers attempt to take out imperfections
in the brush or roller applied membrane finish, to provide a
level and even surface for vinyl installation. Some will slice
off, or grind back ridges and high spots. Other damage
occurs as vinyl installers cut joints for welding in-situ,
such as butterfly corners, directly onto membranes.
3. Moisture build up beneath vinyls where negative pressures
result in membrane failure and adhesive failure - One of
the reasons that we are required to waterproof beneath
vinyl is the presence and build-up of condensation beneath
the vinyl. Hot water to the surface, and cool substrates and
cavities beneath the vinyl result in condensation forming
which can blister membranes and lift solvent based
adhesives. This is why installers of laminate linings and
acrylic sanitary shell products leave the bottom wall/tray
joint open for drainage and silicone seal the top sheet joint
to minimise steam going down behind the sheets. Wall
sheeting is adhesive fixed by applying separated vertical
runs of adhesive, to allow for drainage.
The solution to avoid all of these defects is to install a
complete and compatible membrane/vinyl lining system.
A material compatibility chain, preferably from a single
manufacturer, will go a long way to avoiding compatibility
issues. Documenting of this compatibility chain, as part of the
waterproofing application certificate, is one way to control
this. Builders and project managers should ensure that the
compatibility chain is followed by all, through stage inspections.
A suggested compatibility chain and sequence of
construction is as follows. This should be sought and
documented in writing by your material manufacturer, as a
site specification:
i. Bonded screed to substrate with falls as required by AS
3740. Bonding agent either to be applied beneath screed or
an additive mixed into the screed to form a fully bonded bed.
ii. Negative pressure membrane (possibly a hydro epoxy)
applied to moisture laden green screed. This will avoid
delays in the construction process and resistance to
moisture building up in the screed, from blistering the
topical membrane.
iii.Class III water based membrane to full floor and
appropriate wall application, compatible with finishes and
coverings. This must be accompanied by the appropriate
connector sealants and bond breakers with release zones.
iv.Cementitious feather coat with bonding additive,
to ensure full bond to membrane. This removes
imperfections in the membrane finish and an isolation
6
6:
CodeMark Certificate of Conformity.
Contact:
Andrew is a registered builder in Queensland, N.S.W and
Tasmania, a Cert III Wall and Floor Tiler and Forensic Tiling
Defect Investigator. His company, Armont Rectification
Builders, specialise in solving waterproofing and tiling
defects throughout the country, and are the owners of the
Tile Reglue Injection Method. T.R.I.M is a specialised service
to positively refix loose floor and wall tiles without removal.
material to protect the membrane from abrasive damage,
including cutting of butterfly corners.
v. Negative pressure hydro epoxy to moisture laden green
feather compound. This provides a stable substrate for
solvent based adhesives, isolates the membrane from
solvent adhesive contact, and resists moisture build up in
the feather screed from lifting the solvent based adhesive.
vi.Solvent based adhesive with the required adhesive
contact coverage by the manufacturer.
Steps iv and v should be applied to all areas expecting
contact between the membrane and solvent vinyl glue.
This would include the walls where vinyl may be coved or
other finishes such as lamipanel requiring the application of
incompatible solvent adhesives.
In conclusion, don’t believe rhetoric that is lacking
supportive evidence. Assess the material protective
requirements as specified by the BCA and match these to
the selected welded vinyl. If components require waterproof
protection, and the selected vinyl is only water resistant,
then a compatible waterproofing system needs to be
installed.
It falls onto the shoulders of the builder/surveyor/
certifier/council inspector to READ and ASSESS the
Performance Solution. Protect the building owner and
yourselves from non-compliant Building Solutions.
If it’s not supported in writing, then it’s not true!